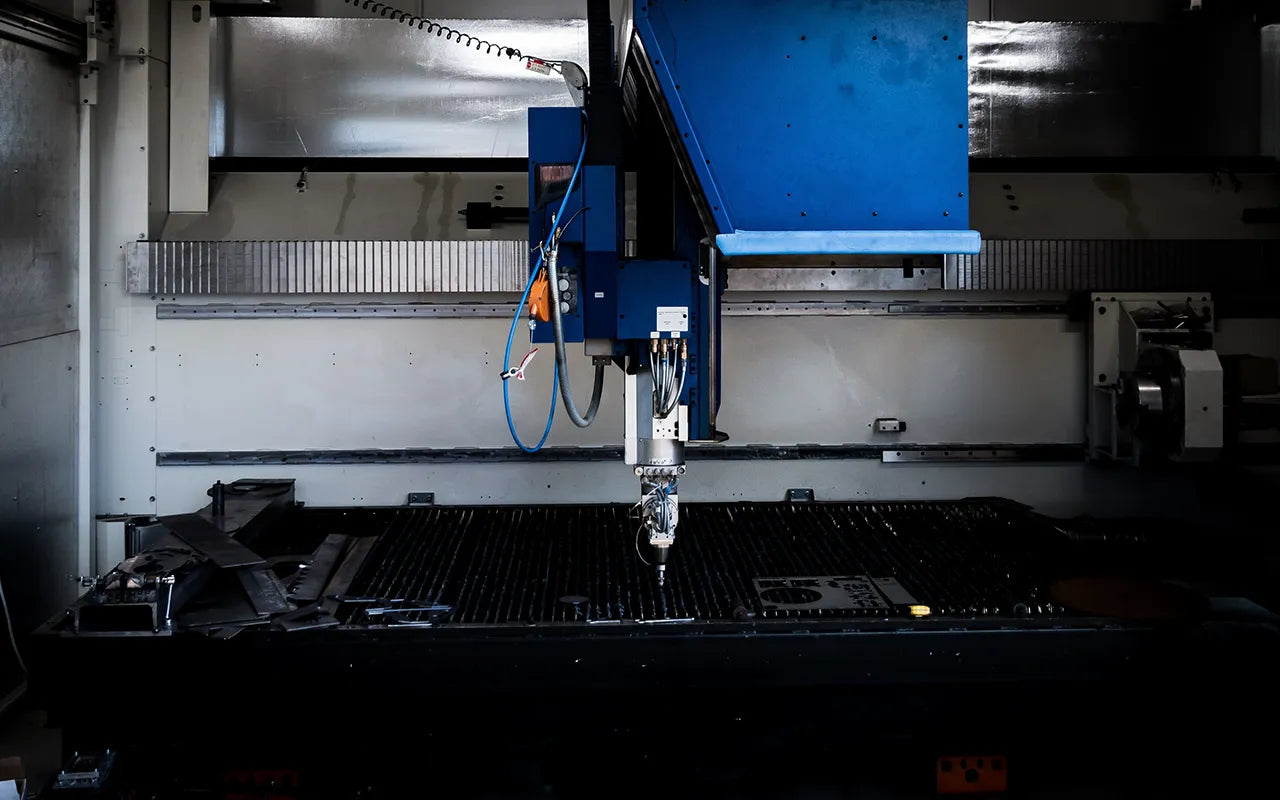
THE WRISTBUDDYS RUBBER STRAP PROCESS
At Wristbuddys, we believe a rubber strap should do more than just hold your watch — it should enhance it. Engineered with exacting precision, our rubber straps are designed to feel like a natural extension of your timepiece, combining durability, comfort, and long-term performance.
From formulation to final fit, every stage of our production process reflects our commitment to quality and craftsmanship.
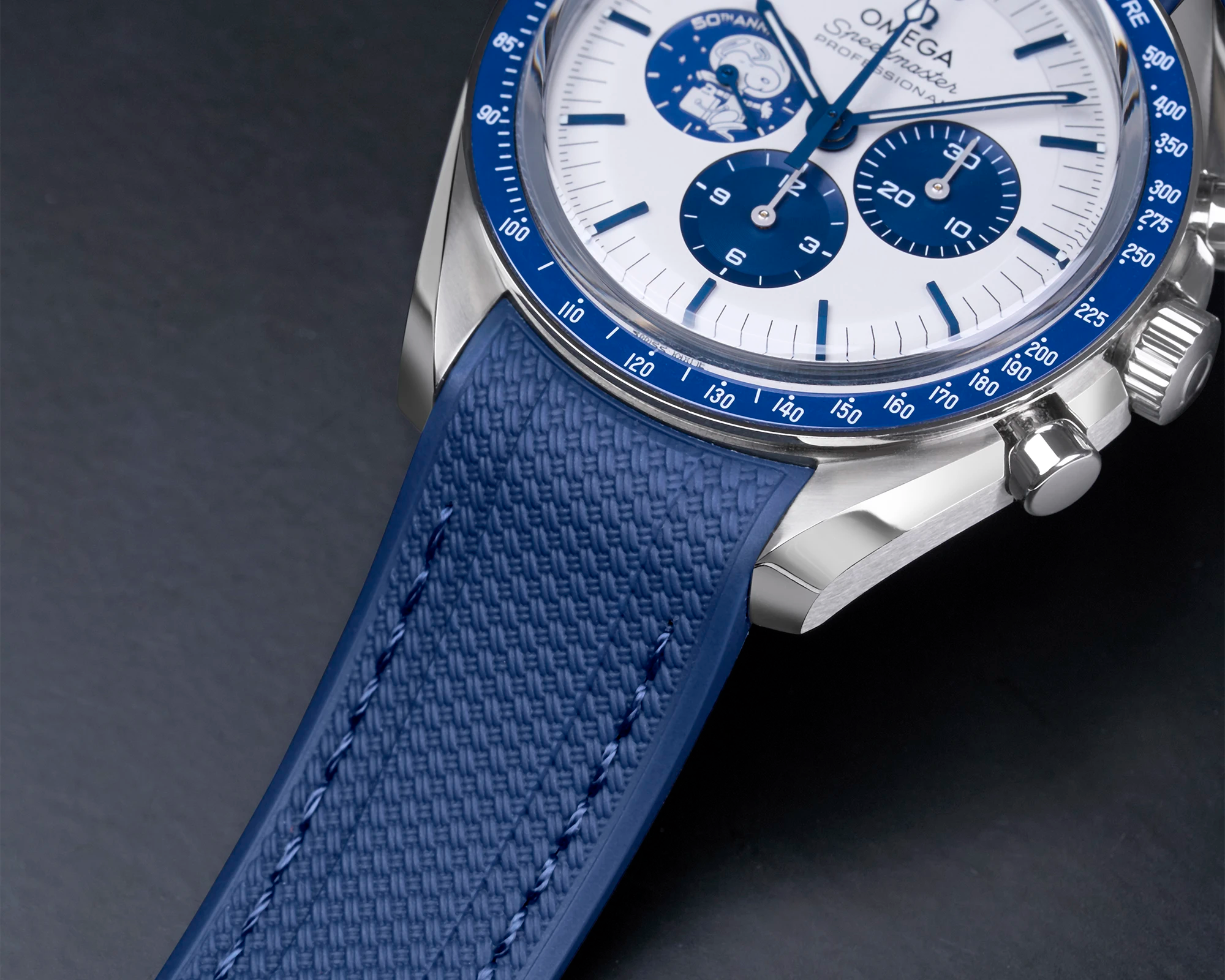
1. 3D SCANNING FOR A SEAMLESS FIT
It all begins with precision. Every rubber strap starts with an ultra-accurate 3D scan of the watch case — capturing every curve, lug, and contour. This ensures flawless integration between strap and timepiece, eliminating gaps, misalignment, or inconsistencies.
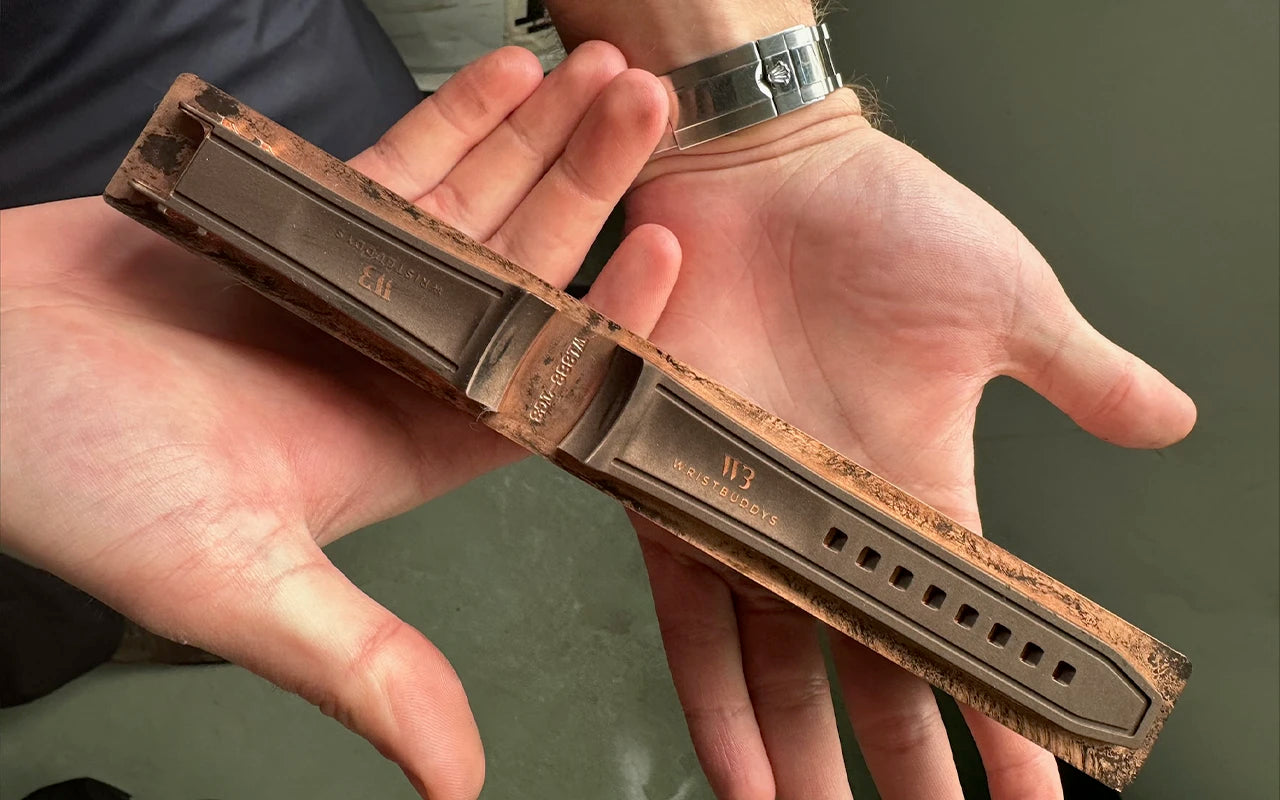
2. 3D DESIGN & PROTOTYPING
Our design team then creates a digital model using advanced CAD software. From lug width to tapering and curvature, every detail is tailored to complement the watch's design. A resin prototype is laser-printed and test-fitted on the actual case — allowing us to refine the strap down to the smallest detail before moving to production.
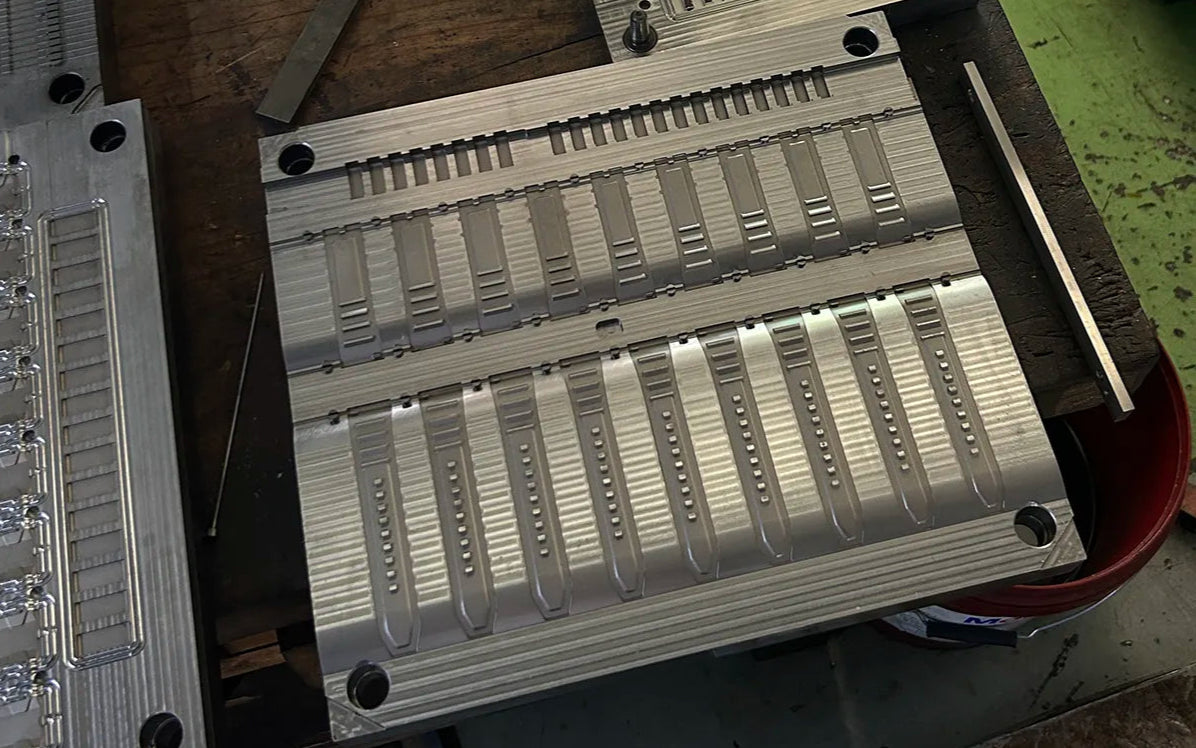
3. MOLD CREATION: CRAFTING THE MASTER TOOL
Once the design is perfected, we begin crafting the mold. Using a solid brass block, we apply high-precision laser welding and EDM (Electrical Discharge Machining) to carve out every dimension. The mold is cooled in water throughout the process to maintain thermal stability and ensure micron-level accuracy. Reinforcements are added to withstand high-volume production without loss of detail.
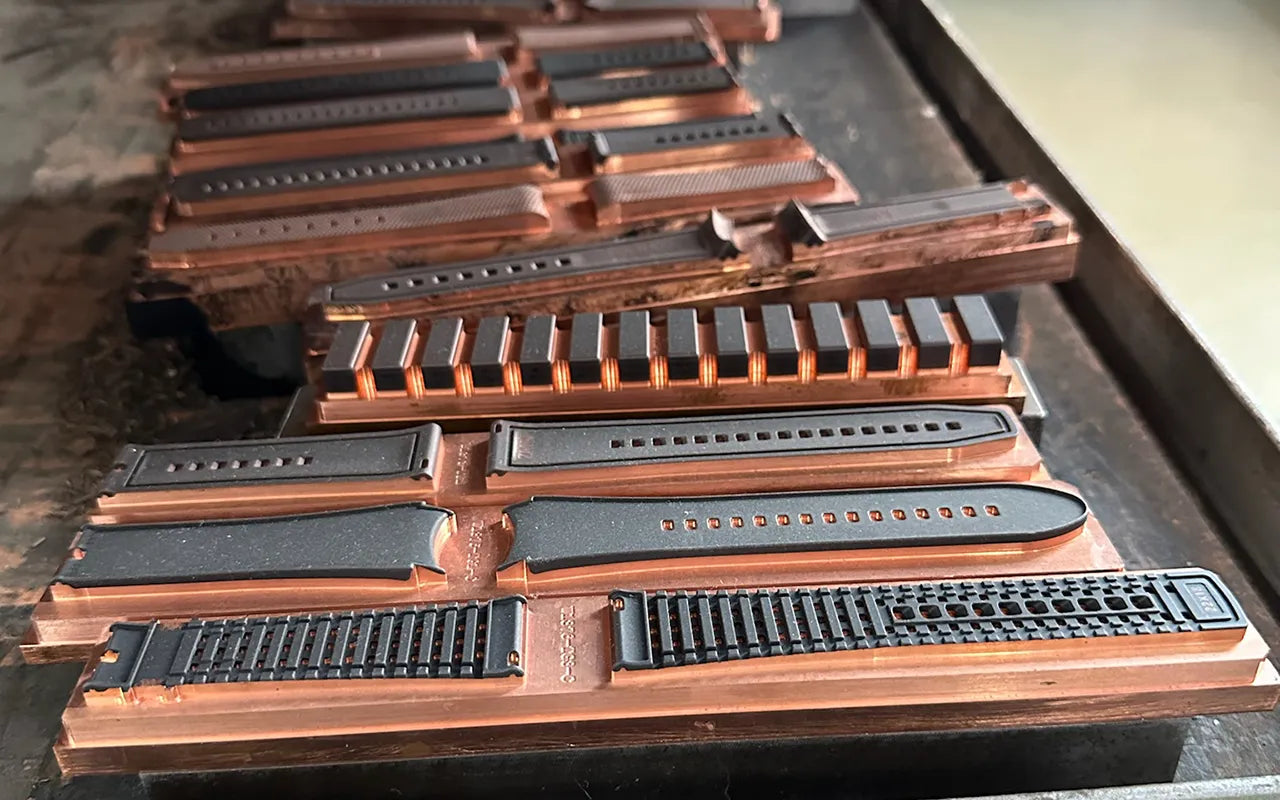
4. STEEL MOLDS FOR PRODUCTION
The finished brass mold serves as the blueprint for our hardened steel molds. These production molds allow us to manufacture multiple straps simultaneously — maintaining consistency, efficiency, and precision at scale.
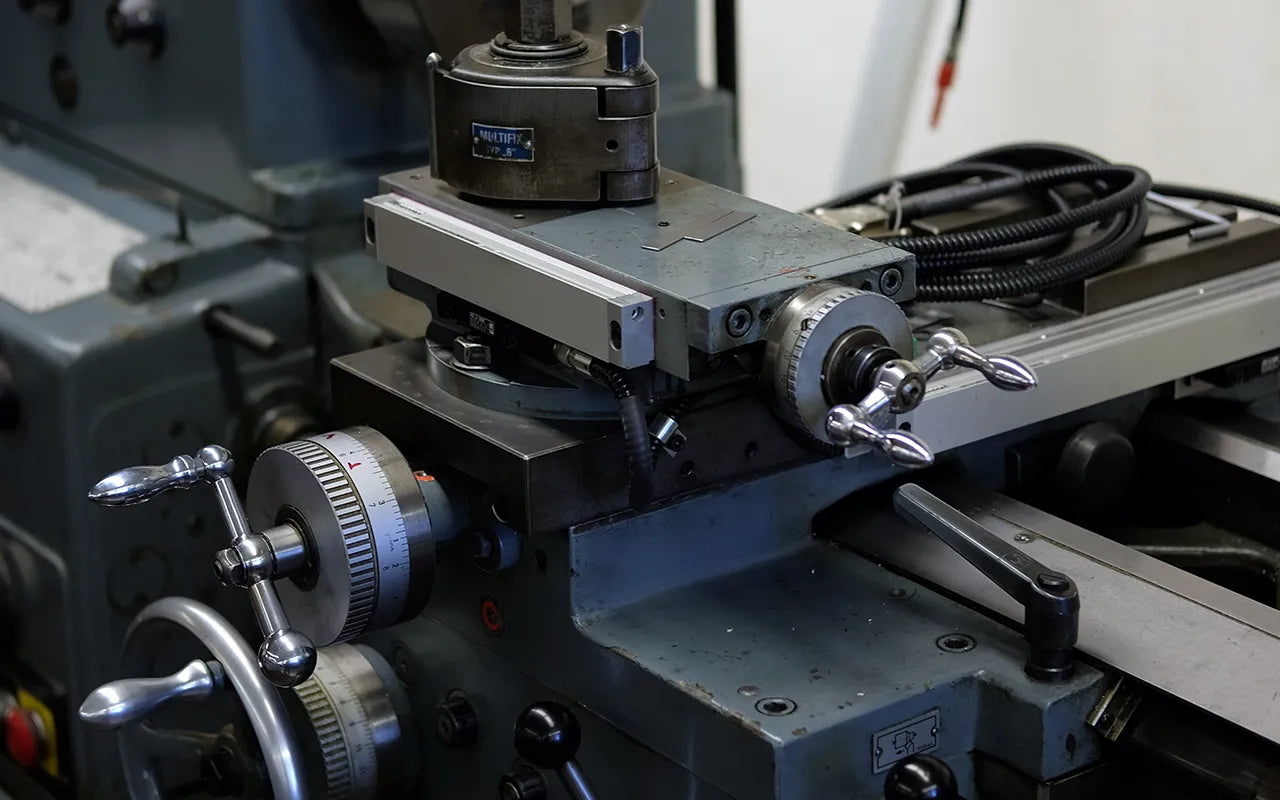
5. RUBBER INJECTION & HEAT PRESSING
With molds ready, pre-measured rubber compounds are injected and heat-pressed under high pressure for five minutes. This ensures even material distribution, eliminates air pockets, and delivers a flawless surface finish with optimal strength and elasticity.
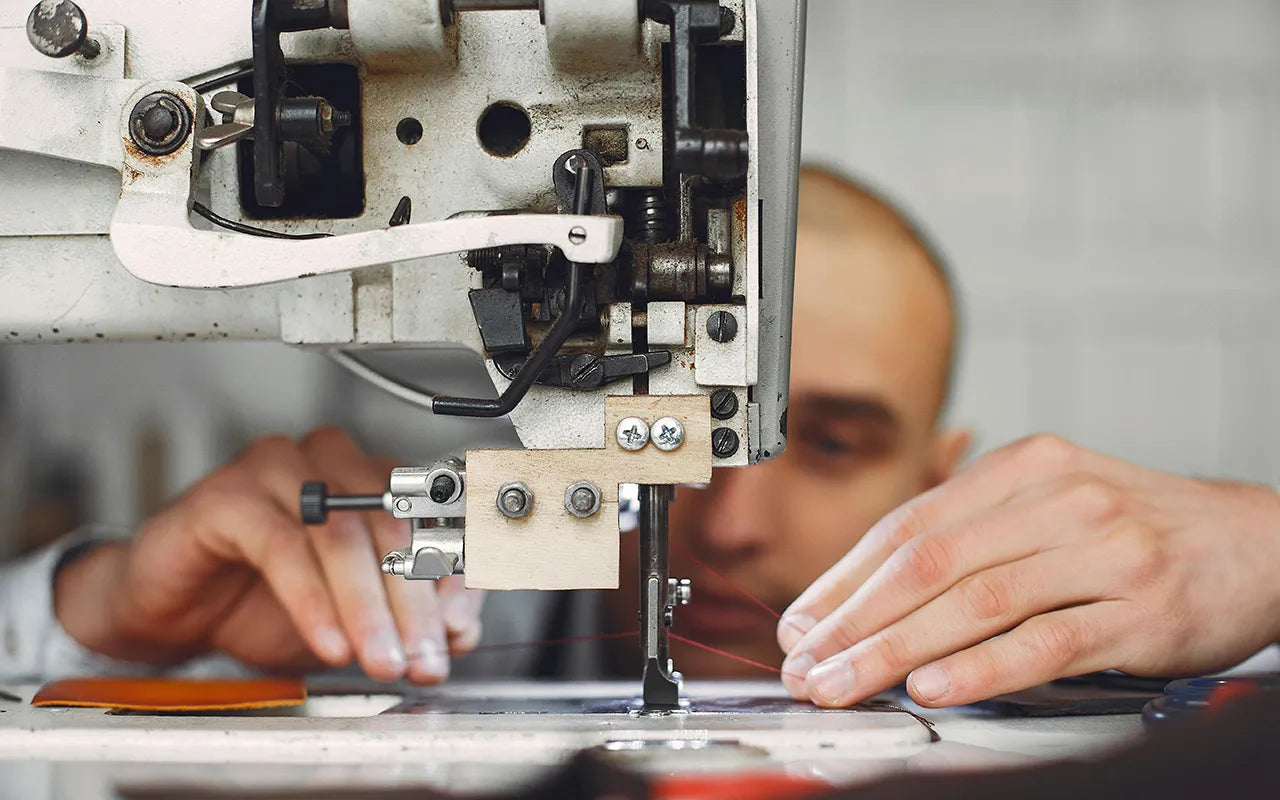
6. HAND-FINISHING FOR PERFORMANCE & COMFORT
Each strap is carefully removed and undergoes detailed hand-finishing. Edges are trimmed and smoothed, surfaces are treated for a soft-touch feel, and every element is refined to strike the perfect balance between durability and comfort.
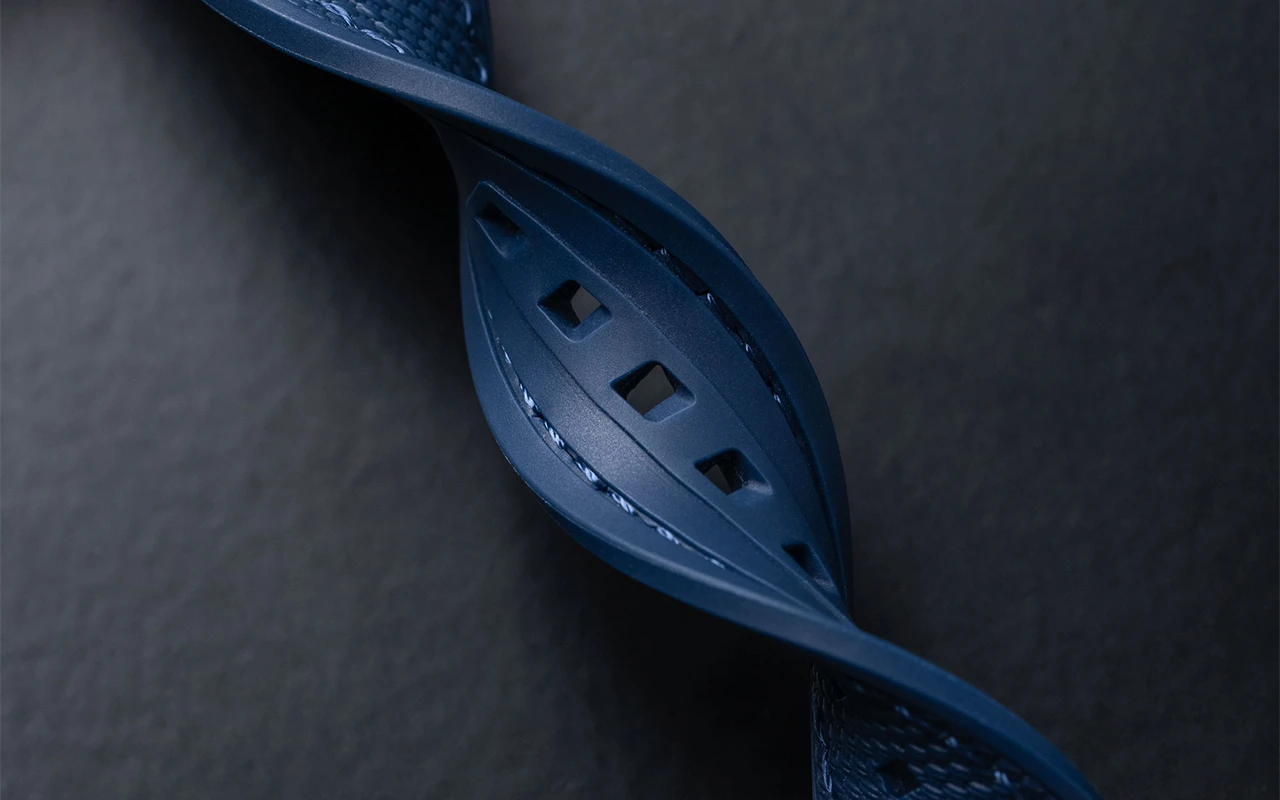
7. RIGOROUS QUALITY CONTROL
Before reaching your wrist, every strap passes a multi-point inspection. We evaluate
- Seamless integration with the watch case
- Uniform texture and finish
- Flexibility, strength, and long-term resilience
Only the straps that meet our exacting standards move on to final packaging.
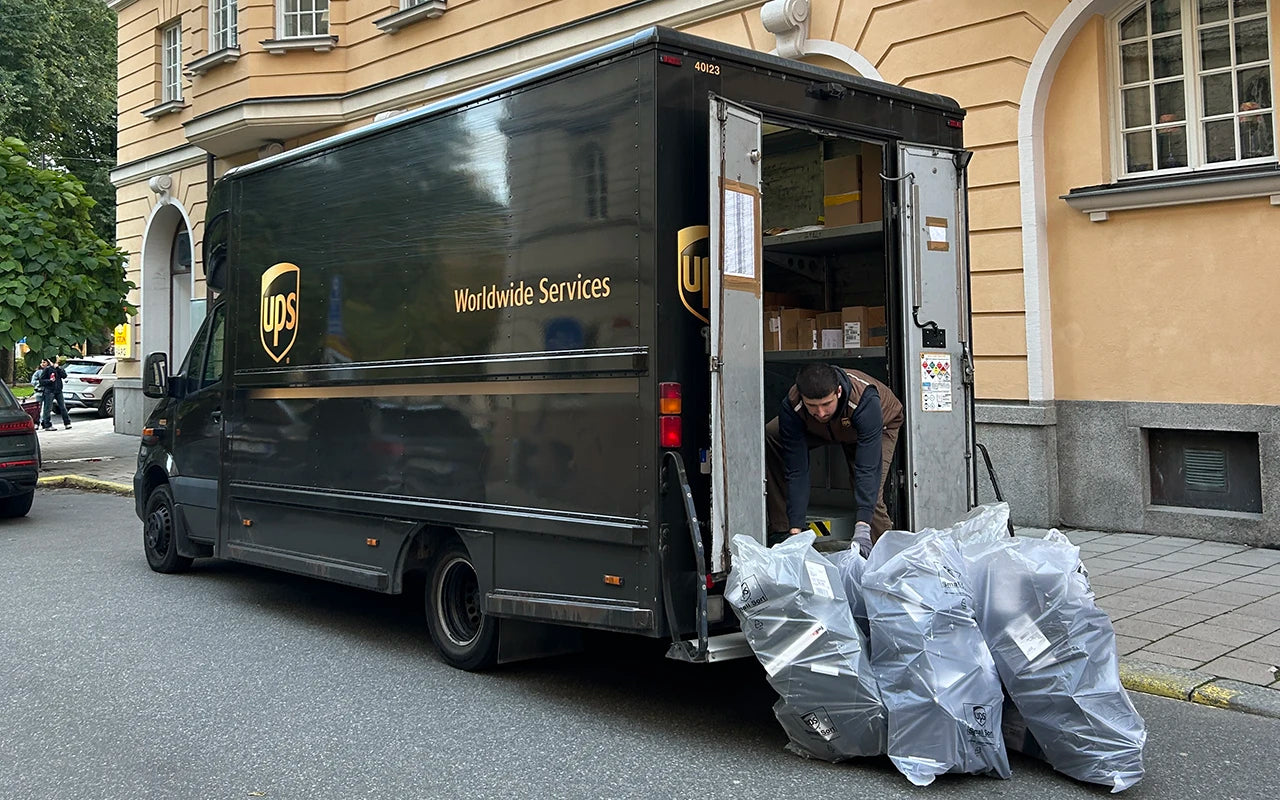
8. PACKAGING & FINAL DELIVERY
Once approved, each strap is carefully packaged at our Stockholm warehouse — ready to be shipped to watch enthusiasts around the world. Our packaging is thoughtfully designed to protect the strap while delivering a premium unboxing experience that reflects the care put into every detail.
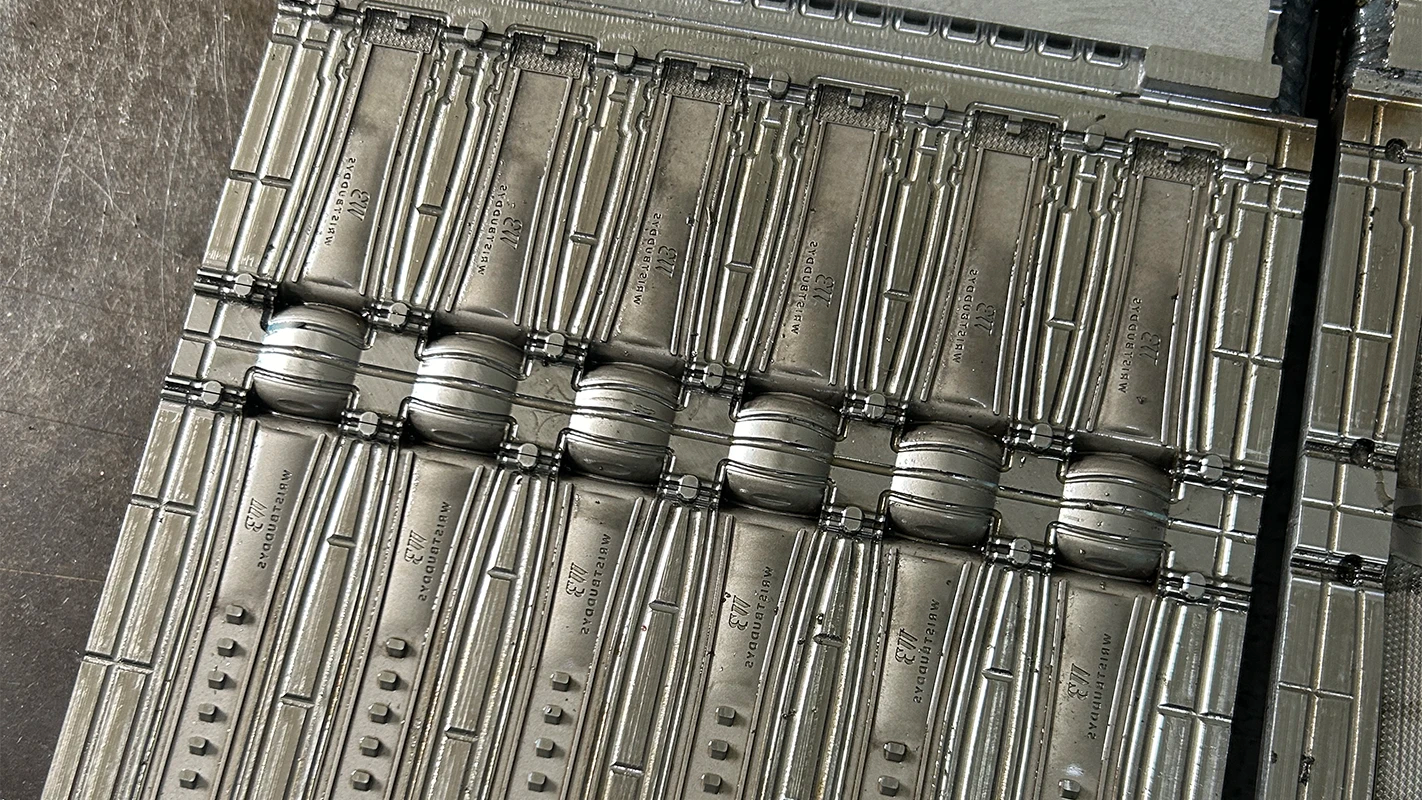
9. ONGOING MOLD MAINTENANCE
Precision doesn’t stop at production. To ensure consistency over time, all steel molds are regularly cleaned, recalibrated, and maintained. This guarantees every batch of straps maintains the exact same fit, finish, and quality.

ENGINEERED FOR EXCELLENCE
Wristbuddys rubber straps are more than just accessories — they're precision-crafted components built to perform. With a seamless fit, long-lasting durability, and uncompromising comfort, they’re designed to elevate both your watch and your experience